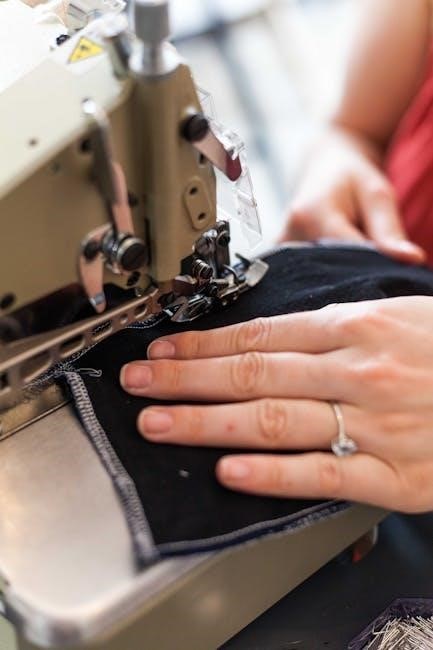
manitowoc ice machine troubleshooting manual pdf
Welcome to the Manitowoc Ice Machine Troubleshooting Manual, a comprehensive guide designed to help users diagnose and resolve common issues with Manitowoc ice machines efficiently.
This manual provides detailed troubleshooting steps, maintenance tips, and essential information to ensure optimal performance and extend the lifespan of your Manitowoc ice machine.
1.1 Purpose and Importance of the Manual
The Manitowoc Ice Machine Troubleshooting Manual is designed to empower users with the knowledge and tools needed to identify and resolve common issues efficiently. Its primary purpose is to provide clear, step-by-step guidance for troubleshooting, ensuring minimal downtime and optimal performance. By following the manual, users can prevent potential problems through proper installation, routine maintenance, and understanding error codes. This resource is essential for maintaining the longevity and efficiency of Manitowoc ice machines, helping users avoid costly repairs and ensuring consistent ice production. Regular use of this manual enables users to address issues promptly, reducing the need for professional intervention and keeping their equipment in top condition.
1.2 Key Features of the Manitowoc Troubleshooting Guide
The Manitowoc Troubleshooting Guide offers a user-friendly approach to diagnosing and resolving ice machine issues. Key features include detailed error code explanations, step-by-step repair instructions, and preventive maintenance schedules. The guide provides interactive access to service manuals, wiring diagrams, and technical bulletins. It covers various models, ensuring comprehensive support for all Manitowoc ice machines. Additionally, the guide emphasizes the importance of water quality and proper installation to maintain efficiency. With clear instructions and essential resources, this manual is an indispensable tool for maintaining optimal performance and extending the lifespan of your Manitowoc ice machine, ensuring reliable operation and high-quality ice production.
Pre-Troubleshooting Checklist
Before troubleshooting, ensure the ice machine is properly installed, powered on, and has adequate water supply. Check for error codes and consult the manual for guidance.
2.1 Understanding Error Codes and Indicators
Manitowoc ice machines use error codes and indicators to signal specific issues, helping you identify problems quickly. These codes, displayed on the machine’s control panel, correspond to detailed explanations in the manual. For example, if the machine fails to run, check for codes like “ICE MACHINE WILL NOT RUN,” which may indicate power issues or component failures. Familiarize yourself with these codes to diagnose problems accurately. Always refer to the troubleshooting manual for code meanings and step-by-step solutions. This feature saves time and ensures effective repairs, preventing further damage to the machine. Regularly reviewing error codes can also help prevent recurring issues.
2.2 Preliminary Checks Before Troubleshooting
Before diving into troubleshooting, perform preliminary checks to ensure the Manitowoc ice machine is operating under optimal conditions. Verify that the machine is properly installed, plugged in, and has a steady power supply. Check the water supply for leaks or blockages and ensure the water filter is clean. Review the installation manual to confirm all settings are correct. Clean the condenser coils and ensure proper ventilation to prevent overheating. Also, inspect the drain system for blockages. These simple checks can resolve many common issues without advanced troubleshooting. Regular maintenance as outlined in the manual can prevent unexpected breakdowns and ensure efficient operation. Always refer to the manual for specific instructions tailored to your model.
Common Issues and Solutions
Identify common problems like the ice machine not running or producing ice. Check power supply, water flow, and filter cleanliness. Routine maintenance often resolves these issues quickly.
3.1 Ice Production Problems: Causes and Fixes
Low ice production can result from insufficient water supply, clogged filters, or high ambient temperatures. Check the water inlet for blockages and ensure the filter is clean. If the machine is in a hot environment, ensure proper ventilation. Additionally, check the condenser coils for dust and clean them if necessary. Faulty sensors or a malfunctioning control board may also affect production. Refer to the manual for diagnostic steps or contact Manitowoc support for professional assistance if issues persist. Regular maintenance can prevent such problems and maintain optimal performance. Always consult the troubleshooting guide for specific solutions.
3.2 The Ice Machine Will Not Run: Possible Reasons
If the ice machine fails to start, check the power supply first. Ensure the machine is properly plugged in and the circuit breaker hasn’t tripped. A faulty switch or malfunctioning electronic control board could also prevent operation. Inspect the wiring for damage or loose connections. Additionally, sensors such as the water level or temperature sensors might be faulty, halting operation. Refer to the manual for specific diagnostic steps or contact Manitowoc support for professional assistance. Regular maintenance, such as cleaning sensors and ensuring proper water flow, can help prevent such issues. Always follow the troubleshooting guide for accurate solutions to restore functionality.
3.3 Low Ice Quality: Troubleshooting and Solutions
Low ice quality can result from improper water temperature, high mineral content, or scaling. Check the water filter for blockages and replace it if necessary. Scale buildup on evaporator plates can reduce efficiency; descale the machine regularly; Ensure the water supply temperature is within the recommended range (usually below 90°F). If ice is cloudy or malformed, inspect the evaporator plate alignment. Clean the machine’s interior and sanitize it to prevent contamination. Refer to the manual for specific cleaning instructions. Addressing these issues promptly can restore ice quality and maintain optimal performance. Regular maintenance is key to preventing such problems.
Maintenance and Cleaning
Routine maintenance and cleaning are essential for optimal performance and hygiene. Regularly descale, clean filters, and sanitize surfaces. Refer to the manual for detailed procedures.
4.1 Routine Maintenance Tasks
Regular maintenance is crucial for ensuring your Manitowoc ice machine operates efficiently. Start by checking and replacing water filters as recommended to prevent impurities from affecting ice quality; Inspect the machine for scale buildup and descale when necessary to maintain proper water flow. Clean the condenser coils regularly to ensure effective heat exchange and prevent overheating. Additionally, check and clean the drain lines to avoid blockages. Lubricate moving parts as specified in the manual to reduce wear and tear. Finally, monitor the machine’s temperature settings and ensure all components are functioning correctly. Following these routine tasks will help extend the machine’s lifespan and maintain optimal performance.
4.2 The Importance of Regular Cleaning
Regular cleaning is essential for maintaining the health, efficiency, and longevity of your Manitowoc ice machine. Dirt, mold, and bacteria can accumulate inside the machine, leading to poor ice quality, unpleasant odors, and even health risks. Cleaning the machine regularly ensures it produces clean, safe ice consistently. Manitowoc recommends using approved cleaning solutions and following the manual’s cleaning schedule to prevent mineral buildup and contamination. Neglecting cleaning can lead to breakdowns, reduced ice production, and costly repairs. Always sanitize the machine after cleaning to maintain hygiene standards. By incorporating cleaning into your routine maintenance, you can ensure your Manitowoc ice machine operates effectively and reliably for years to come.
Advanced Troubleshooting Techniques
Advanced troubleshooting involves detailed diagnostic steps, such as analyzing error codes, inspecting electrical circuits, and checking mechanical components to resolve complex issues efficiently.
5.1 Diagnostic Steps for Complex Issues
For complex problems, start by reviewing error codes and indicators to identify the root cause. Inspect electrical connections, compressors, and condenser coils for damage or blockages. Check water quality and flow rates, as impurities or low pressure can disrupt ice production. Consult the manual for detailed wiring diagrams and diagnostic charts. If issues persist, perform advanced tests on sensors, thermostats, and relays. Document all findings and refer to Manitowoc’s official troubleshooting guide for specific repair procedures. If unsure, contact a certified technician to avoid further damage. Regular maintenance and timely repairs ensure optimal performance and extend the machine’s lifespan.
5.2 Checking Electrical and Mechanical Components
Begin by inspecting the power supply and electrical connections for any signs of damage or wear. Verify that all circuit breakers are functioning correctly and that fuses are intact. Check the compressor, condenser fan, and water pump for proper operation. Ensure all sensors, such as temperature and pressure sensors, are calibrated and functioning accurately. Examine mechanical components like gears and bearings for wear or misalignment. Refer to the wiring diagram in the manual to trace electrical circuits and identify potential faults. If you find any issues, consult the troubleshooting guide or contact a certified Manitowoc technician for assistance. Regular inspections help prevent unexpected breakdowns and ensure smooth operation.
Warranty and Service Information
Understand your warranty coverage for parts and labor, typically covering one year from installation. Proper installation and maintenance are required to maintain warranty validity. Contact Manitowoc service for support.
6.1 Understanding Your Warranty Coverage
Your Manitowoc ice machine is backed by a comprehensive warranty program designed to protect your investment. The standard warranty typically covers parts and labor for one year from the date of installation, ensuring peace of mind. Extended warranties may be available for additional coverage. Proper installation, routine maintenance, and adherence to guidelines outlined in the manual are essential to maintain warranty validity. Repairs due to unauthorized modifications or improper use are not covered. Always refer to your warranty document for specific terms and conditions, as coverage may vary depending on the model and region.
6.2 Contacting Manitowoc Service and Support
For assistance with your Manitowoc ice machine, contact Manitowoc’s dedicated service and support team. Visit the official website at www.manitowocice.com for updated manuals, translations, and contact details of authorized service agents near you. The website also offers an interactive program to access service parts, installation guides, and technical bulletins. If you encounter issues, reach out to Manitowoc’s customer support for professional guidance. Additionally, consult your local Manitowoc distributor for personalized assistance, ensuring prompt resolution to any technical challenges. Their expertise ensures your ice machine operates efficiently and effectively, providing reliable service for years to come.
This manual provides essential guidance for troubleshooting and maintaining your Manitowoc ice machine. For further assistance, visit www.manitowocice.com or contact Manitowoc support.
7.1 Summary of Key Troubleshooting Steps
Troubleshooting your Manitowoc ice machine involves systematic steps to identify and resolve issues efficiently. Always start by checking the power supply, water supply, and drain for blockages or interruptions. Review error codes displayed on the machine, as they provide specific insights into the problem. Clean or replace filters, and ensure proper ventilation to prevent overheating. Regularly inspect and maintain electrical and mechanical components to avoid malfunctions. Refer to the troubleshooting manual for detailed diagnostic procedures and solutions. If issues persist, contact Manitowoc support or a certified technician for professional assistance. Proper maintenance and timely repairs ensure optimal performance and longevity of your ice machine.
For more detailed guidance, visit www.manitowocice.com.
7.2 Further Resources for Assistance
For additional support, visit the official Manitowoc website at www.manitowocice.com to access PDF manuals, service bulletins, and troubleshooting guides. This platform offers comprehensive resources, including wiring diagrams, maintenance tips, and repair instructions. You can also contact Manitowoc’s customer support team directly for personalized assistance. Their dedicated service agents are available to address complex issues and provide expert guidance. Utilizing these resources ensures you have all the tools needed to maintain and repair your Manitowoc ice machine effectively. Explore the website to find updated manuals, technical support, and contact information for authorized service providers in your area.